The Art of Blacksmithing: Bringing the Past into the Present and Future
Posted on Dec 10, 2021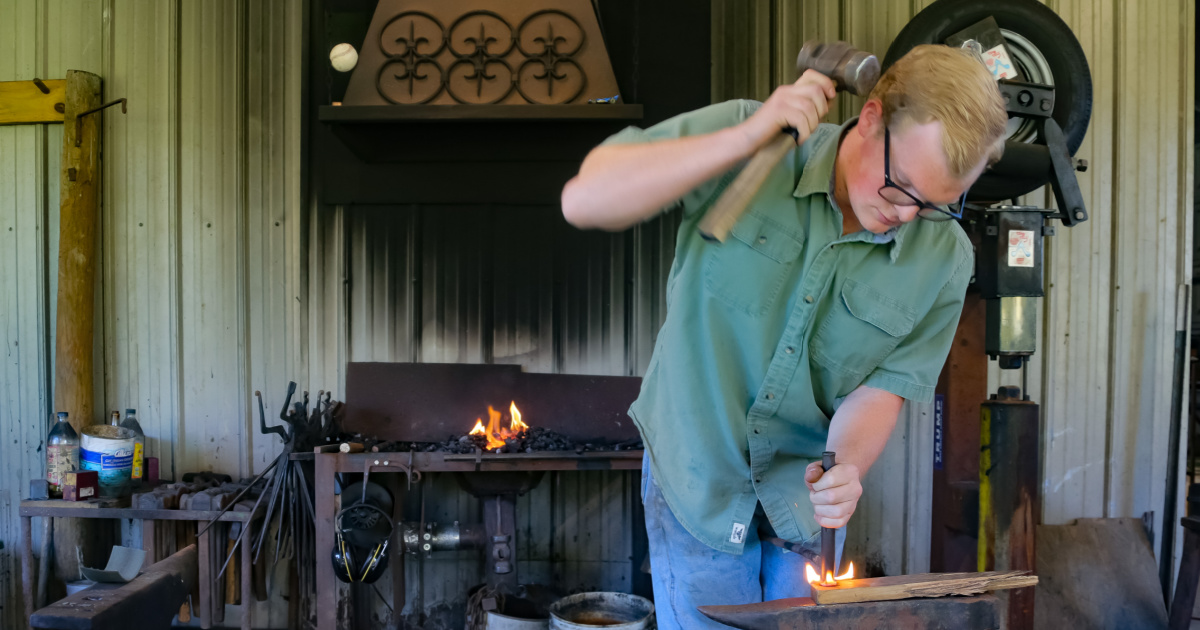
One step into Jonathan Pinkston’s blacksmith shop is like a step back in time. But make no mistake, this Mercer County native is looking toward the future.
The look, smell, and sounds of a blacksmith shop are unmistakable, and very much the same today as they were centuries ago. So it may come as a surprise to see someone as young as Jonathan Pinkston, a student at the University of Kentucky, hammering away on an anvil, creating a multitude of tools in much the same way as blacksmiths have done for generations.
Pinkston, who is also the Kentucky FFA State President, has been blacksmithing since high school as a way to create tools he needed as a woodsman.
“I used to spend a lot of time out in the woods, whether that was hunting or fishing or trapping, camping, or just romping around in the woods behind our house,” he said. “And in spending all that time out there, I used knives and metal hardware. But those were expensive, and I figured I could make some of these implements, whether it would be flint strikers or a knife that I carried in my belt.”
His newfound involvement in making tools for use in the woods grew into a much broader interest in creating his own blacksmith shop. Pinkston’s next step was to take classes to learn more about the art of forging.
“With the same drive I had in making knives and hardware, I dived into the techniques of making tools and equipment for a blacksmith shop,” he said.
One of his teachers, Lyle Wynn, is one of just a handful of craftspeople in this nation who teach this practice of blacksmithing.
“I would say there's about four or five people in the U.S. that teach the same curriculum that I learned; the same curriculum that Lyle Wynn taught to me several years ago,” Pinkston said. “And today, I'm teaching a very similar curriculum in my own shop now. So, I'm one of those four or five people.”
It became obvious early in his blacksmithing endeavors that teaching was in Pinkston’s future. As an ag education major, his future students will likely get a taste of the blacksmith shop.
“This type of curriculum was developed, and has impacted a lot of blacksmiths, especially young blacksmiths who have adopted these techniques for one reason or another, and of course, it ultimately inspired my interest in education going into the future,” Pinkston said.
And while it may seem like the number of those people involved in forging or blacksmithing may be small, Pinkston thinks differently.
“A lot of people would say that blacksmithing or knifemaking is a dying art, but believe it or not, there are more people forging, more people blacksmithing now, than there ever has been in recorded history,” he said. “The reason for that is because, really at this point in time, people are working for a hobby instead of for survival and sustenance. That's how blacksmithing is now.”
Another factor that makes blacksmithing attractive to a younger generation could be the interest they have in crafts Pinkston noted.
“People my age, and younger, are very interested in crafting and doing something technical with their hands,” he said. “And blacksmithing is a really good outlet for that.”
From a technical perspective, Pinkston generally uses a few different types of heat sources which are required in the forging process. These include coal; coke, which is a charcoal-like substance derived from coal; and propane.
Pinkston said what he is making or what kind of metal he is using dictates the type of heat source he will need. He also utilizes anvils, which he can make; an assortment of custom-made hammers; an electric grinder; and a power hammer that was built in the late 1800s and originated in Great Britain.
“While this is an old-style piece of equipment, it is powered now by modern means which brings the old and new together,” Pinkston said. “This particular machine was made in London, England by the Peter Pilkington Limited Company. From my understanding, it made its way to the U.S. in the early 2000s. From there, a man from Minnesota bought it, and I purchased it from him. He never used it so, as far as I know, I'm the first person in the U.S. to ever run the machine.”
Pinkston said an advantage to a shop like his is that he can make about any tool or extra part he may need, much the same way as his predecessors did hundreds of years ago. That’s something that comes in handy, especially on a machine as old as the power hammer.
“It’s like stepping back in time, as far as ideas are concerned, or some of the practices involved. But there's a lot of new and re-discovering taking place, as well,” he said. “In blending old and new techniques, I'm able to honor blacksmiths of the past, while producing these items quicker and more efficiently than they did.”
In sharing his knowledge of forging with others, Pinkston is able to take many of his tools on the road to do various demonstrations, in addition to the classes he holds at the shop.
"I want to be in education, whether that's from a blacksmithing perspective or whether that's as an agricultural teacher in the high school system," he said. “But no matter what form my career takes, blacksmithing will always be a glorified hobby, I guess you could say, and something that I do.”
In true teacher fashion, Pinkston added, “Being a blacksmith, is not necessarily about creating something for people to evaluate or interpret, but instead, re-discovering ideas from the past for people to use now and well into the future.”
Comments